Ford SA makes further multi-million rand investments in Silverton plant
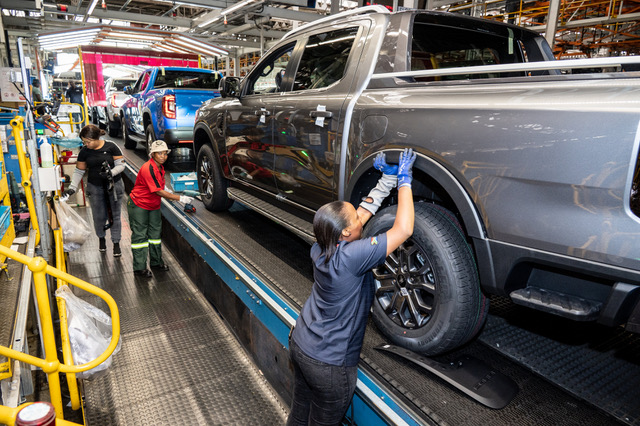
Ford South Africa has made further multi-million rand investments in its manufacturing plant in Silverton, Pretoria, after its initial R15.8 billion investment to expand and upgrade the plant for production of the Next-Gen Ranger.
One of Ford SA’s major investments is a further R22 million spent on a new skid cleaning facility for its advanced paint shop, the first fully automated facility of its kind in the Ford world.
The robotic skid cleaning cell uses extremely high water pressure of 2 500 bar to remove built-up paint residue from the vehicle skids that carry the vehicles through the painting process, allowing for consistent docking and positioning of the body and loadbox on the skid, which ensures optimal paint application.
Read: Ford seen laying off 1 300 workers in China, local media reports
This process greatly reduces the amount of dirt, residue and contaminants entering the paint shop, thereby improving the quality of the paintwork.
Other new investments at the plant include:
R20 million in a new DeGould auto scan shipping tunnel, which replaces in-person inspection of vehicles for misbuilds, damage, or defects smaller than can consistently be found by the naked eye, with automated inspections.
R15 million in a new scrap yard, which will increase the amount of scrap sorted on site and recovered.
R20 million in a new centralised canteen for stamping plant and body shop employees to create a world-class working environment.
R5 million in an on-site laundry facility for the washing of employee personal protective employee (PPE) clothing.
Tim Day, Silverton plant manager at Ford SA, said the customer is at the forefront of the investment in the automatic scanning of all the vehicles produced in the plant, with the facility capturing an image of the entire vehicle in six seconds and detecting defects and damage in 30 to 50 seconds per vehicle.
Images and claims
Day said the images of each vehicle before leaving the plant is an excellent source of data for claims disputes and the investment is aimed at reducing warranty claims by understanding the processes that will rectify defects and damage.
He said this vision technology allows Ford SA to confirm that a specific vehicle did not leave the plant in that condition and it needs to work on the shipping process and for the carrier company and dealer to take responsibility for inspection checks when they accept the vehicle and accountability for any damage.
“Now we have ability to say: ‘No, it’s your fault.’ If they accept that if the car carrier delivers the car with scratches, dings and so on … they’re going to bear that cost plus it’s going drive them to be more disciplined around that part [inspections],” he said.
Recycling
Ockert Berry, vice president of operations at Ford SA, said the company is stepping up its commitment to reducing its impact on the environment by building a new scrap yard.
Day said the scrap includes all packaging that comes into the plant and wood, but could also include scrapped vehicle bodies “especially with the challenge of power”.
Impact of load shedding
He said the plant has not experienced any load shedding because it is in a Special Economic Zone (SEZ) but admitted that Ford SA struggles a lot to keep the plant alive at times because of power dips.
Day said these power dips could be for a millisecond but could leave a vehicle stranded in the E-coat facility because it shuts down every computer and it could take half an hour to reset the command that was being processed by the computer to get the facility back up and running.
He said the plant has reduced its reliance on Eskom “but the fact is, we’re still connected to the grid”.
In May 2022 the Ford Silverton assembly plant switched on its solar project, which uses 3 610 solar photovoltaic (PV) carports to generate 35% of the plant’s electricity requirements as part of the Ford Motor Company’s global sustainability drive to use 100% carbon-free electricity, across all manufacturing operations by 2035. It aims to achieve carbon neutrality by 2050.
Installed capacity
Berry said Ford SA will continue to monitor the situation and look for opportunities to mitigate against potential risks.
The Silverton assembly plant has an installed capacity to produce up to 200 000 vehicles per year.
This is the highest volume yet for this facility, which assembles the Next-Gen Ranger as well as Volkswagen Amarok pickups as part of the Ford-VW strategic alliance.
Based on three-shift 24-hour production, the plant is capable of producing up to 720 vehicles per day.
A total of 29 622 Next-Gen Rangers have been produced at the Silverton plant from December 2022 until the end of May 2023. Total Ranger domestic sales of 7 412 vehicles were recorded over the same period, which excludes 1 766 Next-Gen Ranger Raptors that are now produced in Thailand and fully imported.
Export markets supplied
Between December 2022 and end-May this year, 22 210 Next-Gen Rangers have been shipped to export markets.
Europe has been the largest destination but the Next-Gen Ranger is exported to more than 100 global markets through the roll-on-roll-off (RoRo) terminals at the ports of Durban and Port Elizabeth.